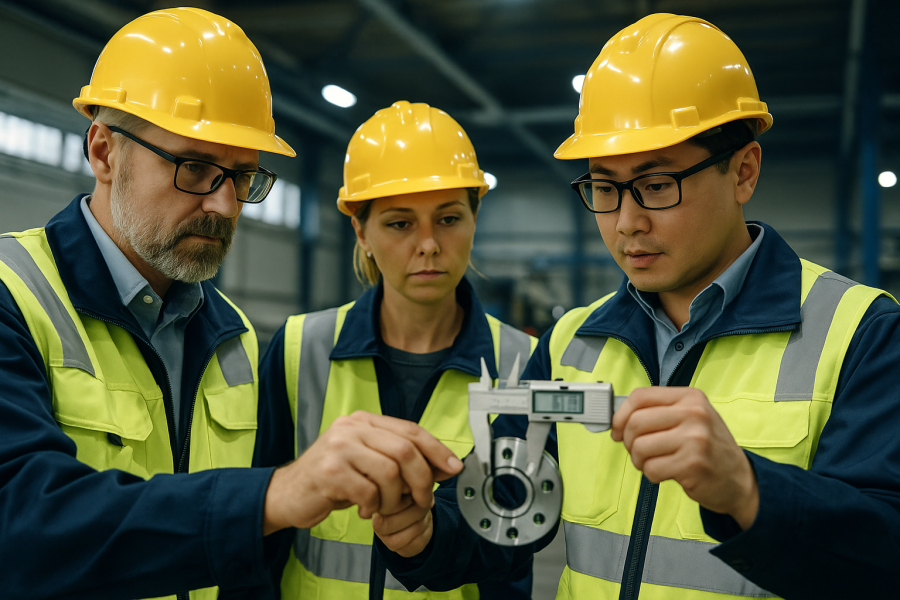
Supply chain disruptions are an unfortunate reality in today’s global manufacturing environment. From late shipments to non-conforming parts, supplier-related issues are among the leading causes of missed deadlines, cost overruns, and product recalls. But what if these risks could be minimized — or even prevented altogether?
That’s where proactive quality engineering comes into play.
Brands that invest in early supplier engagement, hands-on inspections, and continuous improvement strategies are not only avoiding crises — they’re gaining a competitive edge. And at the center of this risk management strategy is a specialized role: the Supplier Quality Engineer (SQE).
In this article, we’ll explore how proactive quality engineering reduces supplier risks and ensures reliable performance across the production lifecycle.
Supplier Risk: More Than Just a Delivery Problem
When people think of supplier problems, they often imagine a late shipment or a missed PO. But risk runs much deeper.
Here are just a few types of supplier-related risks:
Quality Failures: Defective or out-of-spec parts that impact final assembly
Process Instability: Variation in key manufacturing parameters over time
Poor Documentation: Missing or incorrect inspection data and certificates
Lack of Root Cause Analysis: Repeated issues due to weak corrective action systems
Low Engineering Capability: Suppliers unable to interpret technical drawings or resolve issues independently
Each of these issues can cost your business time, money, and credibility. And all of them are avoidable — with the right supplier quality engineering approach.
Proactive vs. Reactive: What’s the Difference?
Many companies only get involved when problems emerge. But by then, it’s often too late — the damage is already done.
Proactive quality engineering means embedding risk controls at the source — long before defective parts reach your plant.
It includes:
Auditing supplier capability before production begins
Implementing PPAP (Production Part Approval Process) and APQP (Advanced Product Quality Planning)
Creating control plans and inspection routines tailored to your specs
Establishing early warning systems for defect trends or process drift
Training supplier teams on quality expectations and engineering protocols
It’s the difference between constantly firefighting — and building a supplier network that runs smoothly from day one.
How Proactive Engineering Prevents Costly Supplier Issues
Let’s break down the key benefits of engineering-led quality oversight at your supplier sites:
1. Early Process Validation
Before production ramps up, proactive engineers work with the supplier to validate the manufacturing process. That includes:
Verifying equipment capability
Checking tooling condition
Reviewing work instructions
Performing trial runs
This ensures the process is stable and repeatable — reducing variability from the start.
2. Design for Manufacturability Checks
SQEs often serve as the bridge between design and production. If a part has features that are difficult to produce, or tolerances that are too tight for available equipment, the SQE can flag this early and propose design or process changes.
This prevents scrap and rework that might otherwise emerge months into the program.
3. Data-Driven Monitoring
Once production begins, supplier quality engineers monitor output using real-time data — such as dimensional reports, SPC charts, or incoming inspection results.
If a negative trend appears, they can act fast — before defects become systemic.
4. Robust Corrective Action Management
When issues do occur (as they inevitably will), proactive engineers drive meaningful corrective action.
Instead of superficial fixes, they lead:
Root cause analysis (often using 5 Whys, Fishbone Diagrams, etc.)
Containment plans
Process changes
Follow-up audits
This prevents recurrence — the ultimate goal of quality management.
A Look Inside a Real-World Example
Let’s say a consumer electronics brand sources injection-molded housings from a factory in northern Mexico. During launch, the first few lots are perfect. But in month three, dimensional variation begins to creep in — causing fitment issues during final assembly.
With no on-site support, this might take weeks to detect. By then, thousands of defective units are in the pipeline.
But with a supplier quality engineer on-site, issues are detected during in-process checks. The SQE traces the root cause to tool wear, works with the supplier’s maintenance team to recondition the mold, and updates the preventive maintenance schedule.
Production continues — no line stoppages, no customer complaints, and no financial loss.
That’s the power of proactive quality oversight.
Why Mexico Is a Top Region for Supplier Risk Management — If Done Right
Mexico is fast becoming a manufacturing powerhouse, particularly in sectors like automotive, aerospace, and consumer goods. With skilled labor, geographic proximity to the U.S., and cost advantages, it’s a smart place to build supply chains.
But risks still exist — especially among new or underdeveloped suppliers. That’s why companies operating in Mexico rely on external engineering support partners to bridge the gap between expectation and execution.
One such partner, AMREP Mexico, specializes in risk reduction through supplier quality engineering.
risk reduction through supplier quality engineering
Their teams of on-site engineers provide technical oversight, supplier coaching, and real-time feedback — helping global brands de-risk their supply chain from within.
Signs You Need Proactive Quality Support
How do you know when it’s time to add engineering oversight at your suppliers?
Watch for these red flags:
Recurring defects from one or more suppliers
Inconsistent quality reports or missing documentation
Late shipments caused by failed inspections
High cost of rework or returns
New suppliers ramping up for critical programs
Limited internal resources to travel and monitor supplier activities
If any of these sound familiar, it's time to build a stronger supplier quality engineering program.
What to Look for in a Quality Partner
Not all engineering support is created equal. Look for these qualities in your quality service provider:
Experienced engineers with backgrounds in your industry
Local teams that understand cultural and regulatory differences
On-site availability — not just remote audits or reports
Ability to implement and follow through on improvement plans
Track record of reducing defects and improving supplier performance
Partners like AMREP Mexico are built for this — helping brands expand their supply base with confidence and control.
Final Takeaway: Risk Doesn’t Have to Be Part of Growth
Scaling your supply chain doesn’t mean sacrificing quality. In fact, the more your operations grow, the more essential it becomes to embed engineering oversight at every supplier touchpoint.
Proactive supplier quality engineering gives you the visibility, control, and responsiveness you need to deliver consistent results — every time.
By investing early in quality processes and people, brands can not only avoid the cost of failure — they can gain the competitive advantage of reliability.
ns216.73.216.109da2